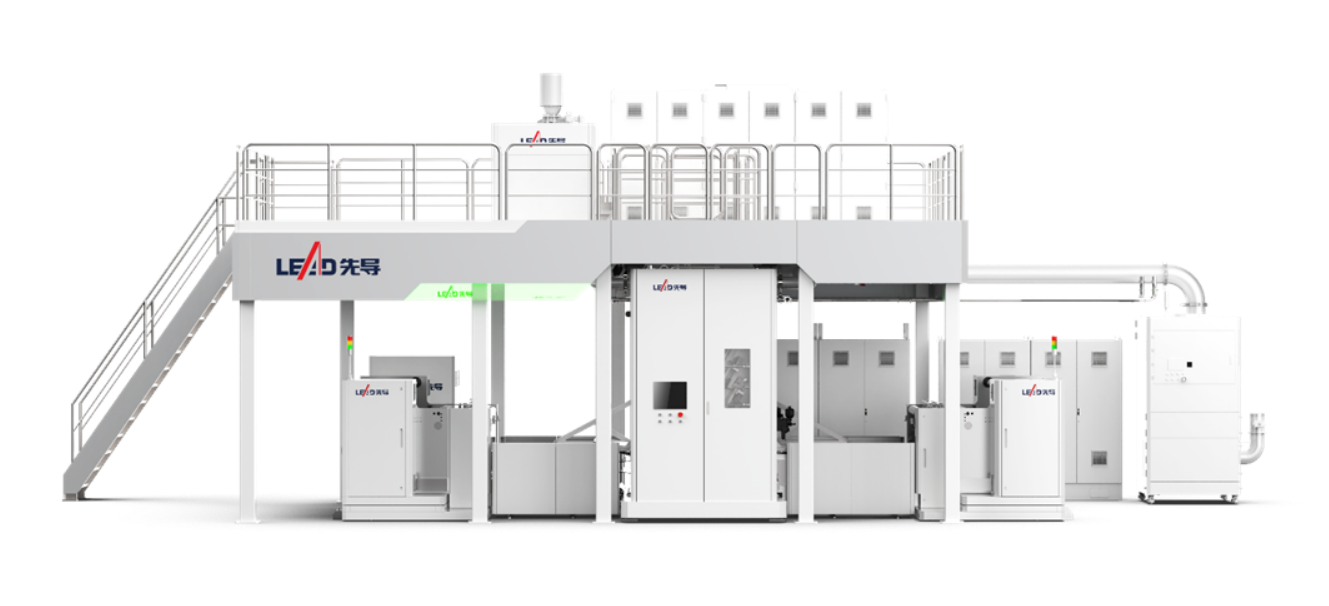
LEAD has officially launched its mass-production integrated dry mixing and coating system for lithium battery anodes and cathodes. Purpose-built for industrial-scale production, the system introduces a solvent-free, energy-efficient solution that sets a new benchmark for clean, high-performance battery manufacturing.
As global battery demand skyrockets and environmental regulations tighten—especially with As coating remains a core process in intelligent battery production, its impact on overall battery performance is critical. While traditional wet coating methods are widely used, the drying stage alone accounts for over 35% of total energy consumption in cell manufacturing. Additionally, solvent use presents ongoing challenges in terms of toxicity, environmental impact, and high recovery costs.
Amid tightening global regulations, rising carbon tariffs, and the industry’s rapid capacity expansion driven by the upcoming 2035 combustion engine ban, dry coating technology is emerging as a key enabler for greener, more economical production. LEAD’s new system is designed to meet this shift head-on.
Designed for Industrial-Scale Throughput and Flexibility
LEAD’s dry coating system supports product widths up to 1000mm, with anode production speeds of 80 meters per minute and cathode speeds of 60 meters per minute. It enables multi-format dry electrode production, aligning with the growing needs of both liquid and solid-state battery manufacturing.
Built on LEAD’s extensive expertise in intelligent equipment for battery production, the system delivers end-to-end process integration, spanning powder unpacking, metering, fiberization, film formation, current collector lamination, waste recovery, and product quality inspection. It represents a complete dry coating solution, optimized for mass production.
Advanced Thermal Control for Lower Energy Consumption
Energy efficiency is a standout feature of the system, thanks to a series of key innovations:
- The industry-first variable-diameter uniform-temperature electric heating system minimizes deformation under load and reduces energy consumption by up to 60% compared to oil-heated systems.
- A three-stage temperature control system for powder fiberization requires only factory cooling water, eliminating the need for mold temperature control units and cutting energy use by approximately 50%.
- Independent roller temperature zones help maintain coating precision and roller rigidity, while improving workshop cleanliness and simplifying maintenance.
End-to-End Process Upgrades for High-Quality Output
To ensure stable, consistent production quality, the system includes:
- Multi-dimensional powder mixing, anti-agglomeration screening, and dynamic pre-mixing to improve coating uniformity
- Edge-cutting recycling, reducing high-value material waste while minimizing airborne pollutants through negative-pressure dust control
- Real-time gap monitoring with ±1μm precision, allowing for automatic online roller adjustment and consistent wide-format balance
Operator-Friendly, Production-Ready Design
LEAD has also prioritized user experience and operational efficiency. The system features:
- Adaptive cutting blades and automated width adjustment, which protect rollers during trimming and accommodate a variety of production formats
- A visual framework design, allowing operators to observe film formation and perform maintenance without the need for climbing or working in tight spaces, enhancing both safety and efficiency
Significant Gains in Efficiency and Cost Reduction
By eliminating solvents and optimizing both thermal and mechanical performance, LEAD’s dry coating system delivers measurable, production-level advantages. It reduces overall energy consumption by more than 35%, while also lowering materials and manufacturing costs by over 20%. These combined efficiencies not only make the system significantly cleaner but also position it as a highly competitive solution in today’s market—one that aligns perfectly with the demands of global battery manufacturers pursuing low-carbon, cost-effective production strategies.